

IKEA mainly uses four different types of unit load carriers:
EUR pallets, Half pallets (600 X 800 mm)
Long pallets (2,000 X 800mm), Corrugated fibreboard pallets.
The half and the long pallets are only used and managed internally at IKEA distribution centres and retail stores.



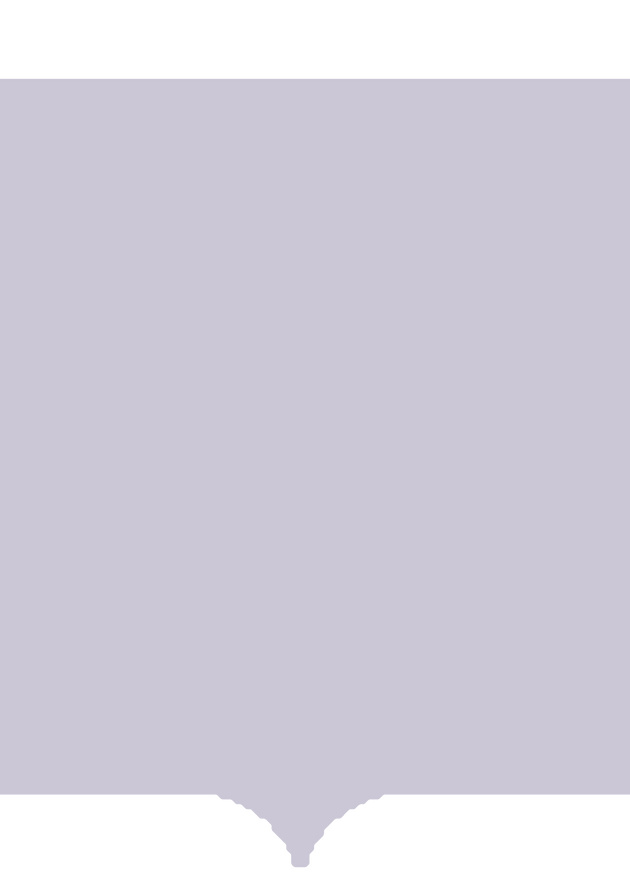
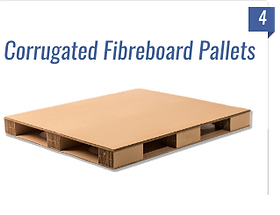

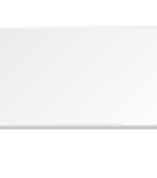
The Use of Loading Ledge
It was first introduced at IKEA in 2001. In 2006, the loading ledge was used for approximately 10 per cent of the total inbound flow. These numbers, however, have continuously risen and in 2010 use of the loading ledge was up to 30 per cent and is expected to reach 40 per cent in 2012.
In IKEA’s packaging, they use loading ledges. Several loading ledges are used to construct a unit load carrier. Depending on how the unit load is shaped, loading ledges are placed in different positions beneath the products. Loading ledges are then strapped to the products and stretch film is applied to the unit load, in order to hold and stabilise it.
The loading ledges are stackable and made of recyclable polypropylene plastic. They are produced using injection moulding and weigh about 370 g each. A loading ledge can handle up to 5,000 kg of static pressure.
The main differences between using loading ledges and a traditional pallet are that loading ledges allow for varying size and design. The use of loading ledges offers the opportunity to adjust the unit load dimensions to specific needs and requirements. For example, adjusting the position of product to fit a traditional pallet, the loading ledge fits accordingly to the products.
Moreover, loading ledges are 45mm high while a wooden pallet is 145mm high (Figure 2).

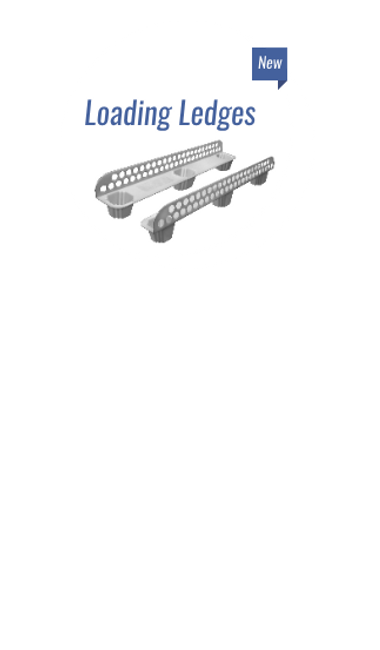

The advantages and disadvantages brought to the different stakeholders.
Manufacturers
Adv: In automated production lines, one result of using loading ledges instead of wooden pallets is that of fewer stops in production. The wooden pallets are often rejected due to their poor quality and this halts production.
Disadv: The shift from traditional pallets to loading ledges would require IKEA to procure new packaging machines.
Transport
Adv: Loading ledges allow unit load dimensions to be adjusted to the products, thereby eliminating empty spaces. Being able to adjust the loading ledges according to the dimensions of the product has also resulted in less damage to products. Fewer empty spaces between the unit leads to less movement, which in turn has decreased the risk of damaging goods.
Disadv: Using traditional pallet, product’s dimension may not fit perfectly with the pallet hence resulting in empty spaces between products.
Distribution centres
Adv: Loading ledges offer better protection from humidity and fork-lift handling, facilitating a more efficient unloading process at distribution centres.
Disadv: It is economically infeasible to change all existing warehouse and material-handling equipment such as conveyors and fork lift which are traditionally designed for wooden pallets to accommodate requirements of loading ledges. In addition, corrugated fibreboard pallets used for sea transportation are easily affected by humid transport conditions, in this mean it might spoil and will be unusable for future usage.
Retail stores
Adv: A great potential in using loading ledges at stores is to improve make the product sales area more appealing. While a majority of incoming goods are directly transported to the sales area, wooden pallets are found to be less appealing for customers.
Recycling/return system
Adv: Loading ledges are used once and are then ground down into plastic pellets. Due to technical advancement of both material quality and production processes IKEA is able to use the pellets as raw material for new loading ledges.
The use of loading ledges drastically reduces the number of return transports and the need for storage space since the loading ledges occupy much less space.
OPERATION INNOVATION #1:
Logistic Driven Packaging Innovation Through the
Use of Loading Ledges
Source:
Daniel Hellström Fredrik Nilsson, (2011),"Logistics-driven packaging innovation: a case study at IKEA", International Journal of Retail & Distribution Management, Vol. 39 Iss 9 pp. 638 - 657


Strength:
1. Reduce packaging time which will also affect
time to market. Similarly, in the BMW case, CAS
was introduced to reduce designing time
Weakness:
1. Might face employees resistance when
adopting this solution. IKEA might have to do
away with manual labours and hence fork lift
operators and other workers might lose their
job.
Whereas in the context of BMW, CAS was
also perceived as a threat to the livelihood of
craftsmen and designers
Similar to

BMW AG:
The Digital Car Project